Torque ripple
The torque ripple in electrical machines is caused by many factors such as cogging torque, the interaction between the MMF and the airgap flux harmonics, or mechanical imbalances, e.g. excentricity of the rotor.
In Emetor, the torque ripple is defined as the percentage of the difference between the maximum torque $T_{max}$ and the minimum torque $T_{min}$ compared to the average torque $T_{avg}$: $$\frac{T_{max}-T_{min}}{T_{avg}}\cdot 100$$ In Fig. 1 you can see an example of how the torque ripple is calculated in Emetor.
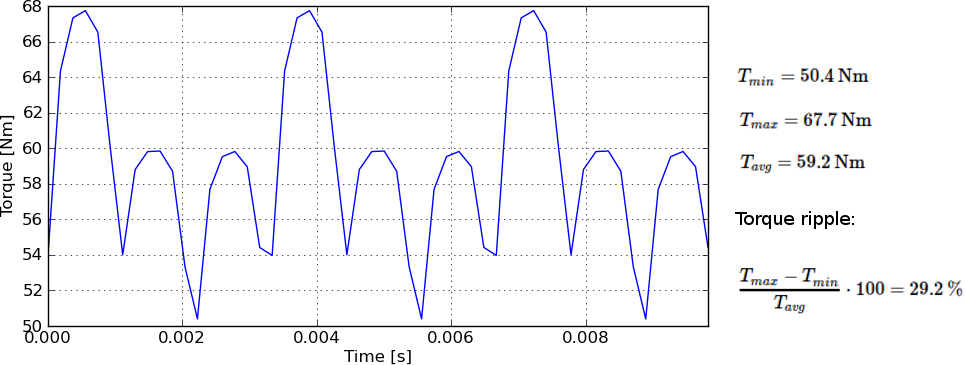
Fig. 1 Example of torque ripple calculation in Emetor.
Torque ripple in electrical machines is generally undesirable, since it causes vibrations and noise, and might reduce the lifetime of the machine. Extensive torque ripple can require measures such as skewing or changes to the machine geometry that might reduce the general performance of the machine. Below you can read more about the two main factors that cause torque ripple:
Torque ripple by cogging torque
Cogging torque in permanent magnet synchronous machines is due to the interaction between the magnetic field of the permanent magnets and the stator slots, which causes variations in the reluctance depending on the rotor position. In order to reduce the cogging torque, you should generally be choosing a winding layout with a large least common multiple between the number of poles and the number of slots. The cogging torque depends also on other parameters such as the slot opening width, eventual magnet width, skewing, etc.
Torque ripple by the interaction between the MMF and the airgap flux harmonics
Under load, there is an additional component contributing to the torque ripple in addition to the cogging torque: Torque ripple due to the interaction between the magneto-motive force (MMF) and the airgap flux harmonics. This component can be influenced by changes to the geometry of the machine design, especially the number of stator slots, the number of poles, the magnet angle, and the slot opening width are important parameters to have a look at.
Conclusions
The torque ripple depends a lot on the winding layout, choice of the magnet angle, and the slot opening width. For surface-mounted permanent magnet machines, the torque ripple is often relatively low for a magnet angle of around 120 electrical degrees, which eliminates the third harmonic in the airgap flux density.
Please keep in mind that a machine with a low cogging torque might have a high torque ripple whereas a machine with a high cogging torque might have a low torque ripple. This is due to the fact that the torque ripple due to the interaction between the MMF and airgap flux harmonics can compensate or increase the cogging torque in different cases.
Read about another glossary term